Warum Rohrlaser?
Laserbearbeitung von Rohren und Profilen erfolgt derzeit fast ausschließlich auf 2D- Flachbettanlagen mit Drehachse. Dabei muss das zu schneidende Rohr immer über die gesamte Teilelänge zuzüglich eines Sicherheitsabstandes zum Drehfutter ausgespannt werden.
Fehler im Ausgangsmaterial wirken sich so unmittelbar und gravierend auf Genauigkeit und Qualität des Endproduktes aus. Dreht sich etwa das Rohr nur wenige Zehntel-Millimeter außer der Mitte, so addieren sich die Maßabweichungen auf gegenüberliegenden Seiten und ergeben dann oft Gesamtabweichungen im Millimeterbereich. Eine lasergerechte Konstruktion ist so kaum umsetzbar.
Mögliche Fehler
Längenfehler
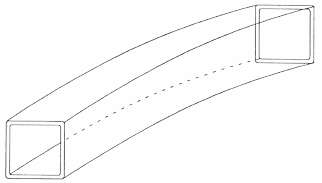
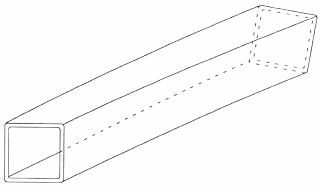
Querschnittsfehler
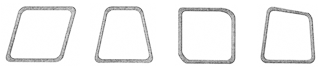
- Parallelogrammförmig
- Trapezförmig
- Unterschiedliche Kantenradien
- Allgemeiner Winkelfehler
All diese Ungenauigkeiten können von 2D-Flachbett-Lasermaschinen kaum kompensiert werden, was einen enormen Einrichteaufwand und damit hohe Bearbeitungszeiten und Kosten zur Folge hat.
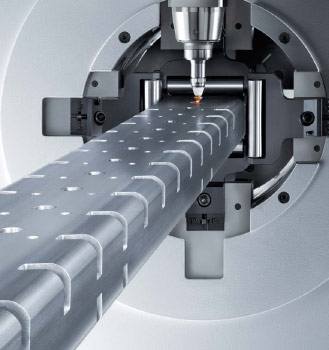
Auf unserer Lasertube 7000 werden Rohre und Profile mit Hilfe eines ‚Durchschiebefutter‘ immer unmittelbar vor dem Schneidkopf zentriert. Damit können Teile bei minimalen Durchlaufzeiten präzise und wiederholgenau gelasert werden.
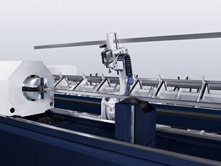
Weitreichende Automation:
… vom Laden aus dem Rohrbündel über hauptzeit-paralleles Vermessen von Querschnitt und Stangen-länge bis hin zur Schweißnahterkennung und sortierter Ablage von Fertigteilen…
senken die Durchlaufzeiten auf ein Minimum und ermöglichen kürzeste Lieferzeiten.
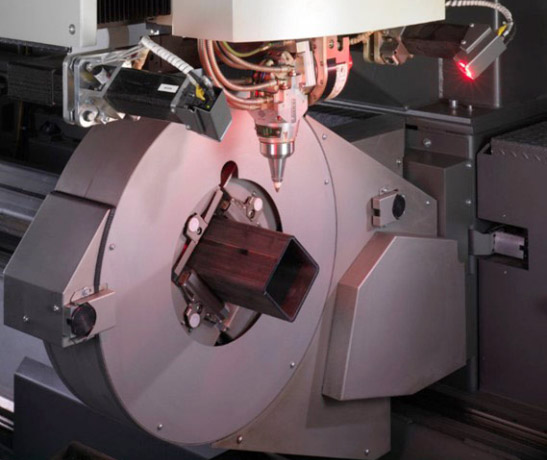
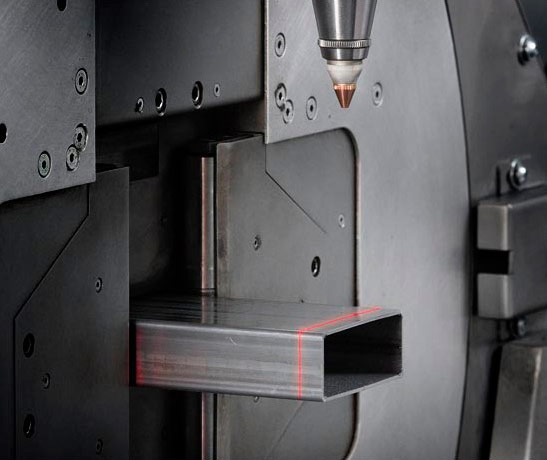
Profile und Rohre sind faszinierende Ausgangsmaterialien mit nahezu unbegrenzten Möglichkeiten. Bei gleichem Materialeinsatz sind sie immer stabiler als Vollmaterial. Damit werden Konstruktionen leichter und fester. Oft sind bei der herkömmlichen Bearbeitung zahlreiche Arbeitsgänge zu verrichten, die mittels Rohrlaser zu einem Schritt zusammengefasst werden können:
Konventionalle Fertigung vs. Rohrlaser
Konventionelle Fertigung:
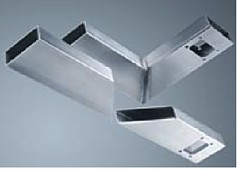
- Sägen
- Anreißen/ Körnen
- Bohren
- Fräsen
- Fasen zur Schweißvorbereitung
- Senken, z. B. für Senkkopfschrauben
- Entgraten
- Vorrichtungserstellung
- Organisationsaufwand (Personal, Software)
Fertigung mittels Rohrlaser:
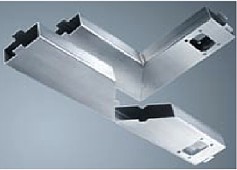
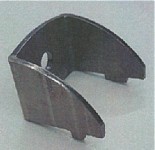
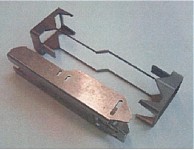
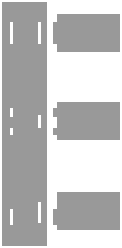
- Lasergerechte Konstruktion möglich (Knickverbindungen, Positionierhilfen usw.)
- Weniger Einzelteile erforderlich
-
Minimierung nachfolgender Arbeitsgänge
Beispiel Schweißen:- Wegfall von Nähten durch Knickverbindungen oder Zusammenfassung von Teilen
- Weniger Schweißarbeit durch geringere Spalte
- Senkung des Aufwandes für Verputz- und Richtarbeiten
- Montagevorrichtung im Teil integriert
-
Zeichnungserstellung stark vereinfacht oder ganz überflüssig
-
Zusammenbau durch Codierungen oder gelaserte Fügehilfen selbsterklärend
→ Montagefehler nicht mehr möglich -
Minimaler Bemaßungsaufwand, da nur noch wenige Funktionsmaße nötig
→ Zeichnung übersichtlicher
-
Zusammenbau durch Codierungen oder gelaserte Fügehilfen selbsterklärend
- Organisationsaufwand deutlich verringert, da weniger Arbeitsgänge erforderlich
- Effizient von Losgröße 1 bis hin zu Großserien
- Biegeteile alternativ aus Rohr